Porosity in Welding: Identifying Common Issues and Implementing Best Practices for Avoidance
Porosity in welding is a pervasive problem that typically goes unnoticed until it triggers significant troubles with the integrity of welds. In this discussion, we will explore the essential factors adding to porosity development, examine its harmful effects on weld performance, and discuss the ideal practices that can be embraced to minimize porosity incident in welding procedures.
Typical Root Causes Of Porosity
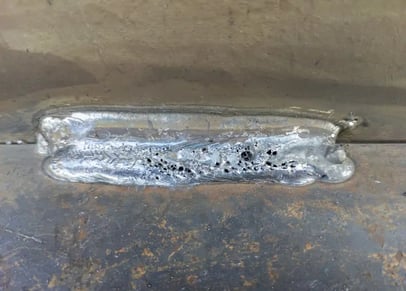
Utilizing unclean or damp filler products can present contaminations right into the weld, adding to porosity issues. To alleviate these usual causes of porosity, extensive cleaning of base metals, proper securing gas selection, and adherence to optimum welding parameters are vital techniques in attaining top quality, porosity-free welds.
Impact of Porosity on Weld Quality

The presence of porosity in welding can substantially compromise the architectural honesty and mechanical homes of welded joints. Porosity develops spaces within the weld metal, compromising its overall strength and load-bearing ability. These gaps work as tension concentration points, making the weld a lot more prone to cracking and failing under applied lots. Furthermore, porosity can minimize the weld's resistance to deterioration and other ecological factors, even more diminishing its durability and performance.
Among the primary consequences of porosity is a reduction in the weld's ductility and strength. Welds with high porosity degrees often tend to display reduced influence strength and lowered capacity to deform plastically prior to fracturing. This can be particularly worrying in applications where the welded components undergo vibrant or cyclic loading problems. Porosity can impede the weld's capacity to successfully transfer forces, leading to early weld failure and potential safety and security threats in vital frameworks. What is Porosity.
Finest Practices for Porosity Avoidance
To improve the architectural stability and top quality of welded joints, what details steps can be executed to lessen the occurrence of porosity throughout the welding procedure? Porosity avoidance in welding is essential to ensure the honesty and stamina of the last weld. One reliable practice is correct cleansing of the base steel, removing any contaminants such as corrosion, oil, paint, or moisture that could lead to gas entrapment. Ensuring that the welding tools is in good condition, with his response tidy consumables and proper gas circulation prices, can additionally dramatically minimize porosity. Furthermore, maintaining a stable arc and managing the welding specifications, such as voltage, existing, and take a trip speed, assists produce a consistent weld swimming pool that lessens the threat of gas entrapment. Making use of the right welding method for the particular product being bonded, such as adjusting the welding angle and weapon setting, can further stop porosity. Regular assessment of welds and instant remediation of any kind of issues recognized throughout the welding process are necessary techniques to stop porosity and generate premium welds.
Value of Proper Welding Strategies
Applying proper welding techniques is critical in ensuring the architectural integrity and top quality of welded joints, constructing upon the foundation of efficient porosity prevention steps. Too much warmth can lead to boosted porosity due to the entrapment of gases in the weld pool. Additionally, using the appropriate welding criteria, such as voltage, existing, and take a trip speed, is essential for attaining sound welds with marginal porosity.
Moreover, the option of welding process, whether it be MIG, TIG, or stick welding, should line up with the Visit Website particular demands of the project to guarantee optimal results. Correct cleansing and prep work of the base steel, in addition to picking the ideal filler product, are additionally essential components of skillful welding techniques. By sticking to these ideal methods, welders can reduce the risk of porosity development and create top quality, structurally audio welds.

Checking and Quality Assurance Steps
Quality control procedures play an essential role in validating the integrity and dependability of welded joints. Testing treatments are necessary to detect and prevent porosity in browse around here welding, ensuring the stamina and longevity of the end product. Non-destructive testing approaches such as ultrasonic screening, radiographic testing, and aesthetic examination are frequently employed to recognize prospective problems like porosity. These techniques enable the assessment of weld top quality without compromising the integrity of the joint. What is Porosity.
Post-weld examinations, on the various other hand, evaluate the final weld for any kind of flaws, consisting of porosity, and verify that it satisfies specified criteria. Implementing a comprehensive quality control strategy that consists of complete screening procedures and evaluations is critical to lowering porosity concerns and guaranteeing the general high quality of bonded joints.
Conclusion
To conclude, porosity in welding can be a common problem that affects the high quality of welds. By identifying the typical root causes of porosity and executing best techniques for avoidance, such as proper welding techniques and screening steps, welders can make sure high top quality and reliable welds. It is vital to prioritize avoidance approaches to minimize the incident of porosity and maintain the integrity of bonded frameworks.